Low power consumption
RBRlegatoยณ C.T.D
Multi-channel instrument for gliders and AUVs
The RBRlegatoยณย C.T.D offers a new world of measurement opportunities for gliders and AUVs. Optimised for flow dynamics, the instrument requires no pump to obtain fine structure measurements. The RBRlegatoยณย provides high accuracy while consuming less power due to modern electronic design and the lack of moving parts.
- Rated to 1000dbar
- Pump-free design with optimized flow dynamics
- Ultra-low power consumption
- Up to 16Hz sampling
- Accurate conductivity to within 10cm of the air-ocean interface
- Unaffected by surface contaminants or freezing conditions
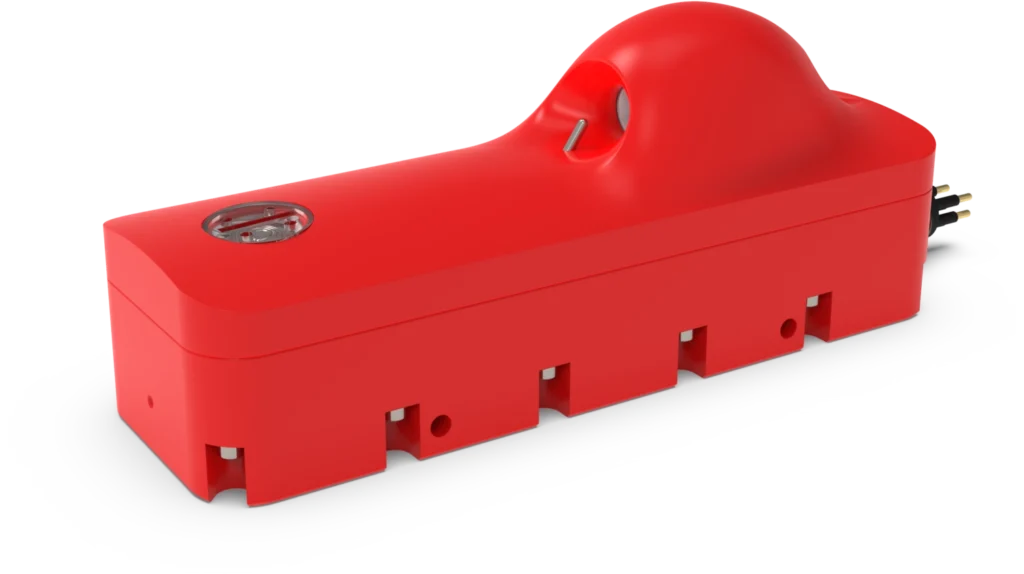
Features
Legato means smooth and connected. The RBRlegatoยณย design and low-power operation is optimized for gliders and AUVs. The CTD is used to derive salinity, density, and sound velocity. The RBRlegatoยณย measures conductivity using a rugged inductive cell that is not affected by surface contaminants or freezing conditions. The CFD-optimised, low aspect ratio conductivity cell is self-flushing and does not require a pump. Using only 45mW when sampling at 2Hz or faster, and 18mJ/sample at 1Hz or slower, the power requirement is 90% lower than traditional pumped CTD sensors. When power management is critical to your mission, the lower power operation permits substantially longer deployments or higher resolution measurements. Totally silent operation is optimized for passive acoustic listening and turbulence measurements. The RBRlegatoยณย is designed to fit into a standard 2″ x 7″ sensor bay and is rated to 1000m.
The RBRlegatoยณย can seamlessly integrate and control your additional sensors. Using the standard RBR building-block system architecture, additional sensors such as dissolved oxygen, fluorescence, turbidity, and PAR are all supported. This sensor-hub design permits efficient system integration for vehicle integrators and users.
About the sensors
Conductivity is measured with an inductive sensor, suitable for deployment in marine, estuarine, or fresh water. There are no exposed contacts, which increases robustness, avoids susceptibility to surface contamination, and allows it to be frozen into ice without damage.
The temperature sensor is built and calibrated in-house using an aged thermistor. The temperature channel is calibrated an accuracy of ยฑ 0.002ยฐC (ITS-90) over the range -5 to +35ยฐC. Extended range calibrations are available.
Pressure is measured with a piezoresistive transducer built with a nickel-based superalloy diaphragm to avoid corrosion. Accuracy is 0.05% of the full scale rating and resolution is 0.001%.
Optional configurations
Design integration | For installation in wet sensor bay |
---|---|
Available sensors | Conductivity (C), Temperature (T), Pressure (D), Optical Dissolved Oxygen (ODO), Photosynthetically Active Radiation (PAR), Radiometer (rad), Turbidity (Tu), Backscatter (bb), Chlorophyll a, Fluorescence (Fl), pH, Transmittance |
Specifications
Storage | 240M readings |
---|---|
External power | 4.5-30V |
Communication | RS-232 |
Clock drift | ยฑ60 seconds/year |
Depth rating | 1000m |
Housing | OSP |
Length | 195.8mm |
Width | 63.8mm |
Height | 78.6mm |
Top Curvature | โ220mm or โ124mm |
Weight | ~0.8kg in air ~0.2kg in water |
Sampling speed | Up to 2Hz (16Hz optional) |
Range | 0-85mS/cm |
---|---|
Initial accuracy | ยฑ0.003mS/cm |
Typical stability | 0.010mS/cm/year |
Resolution | 0.0001mS/cm |
Range | -5ยฐC to 42ยฐC |
---|---|
Initial accuracy | ยฑ0.002ยฐย (-5 to +35 ยฐC) |
ย | ยฑ0.004 ยฐC (+35 to +42 ยฐC) |
Resolution | <0.00005ยฐC |
Time constant | <1s (standard) or <0.1s (|fast16) |
Typical stability | 0.002ยฐC/year |
Range | 1000dbar |
---|---|
Initial accuracy | ยฑ0.05% full scale |
Resolution | 0.001% full scale |
Time constant | <0.01s |
Typical stability | 0.05% FS |
โค1Hz sampling | 22.8mJ per sample |
---|---|
โฅ2Hz sampling | 46mW |
Sleep power | 180ยตW |
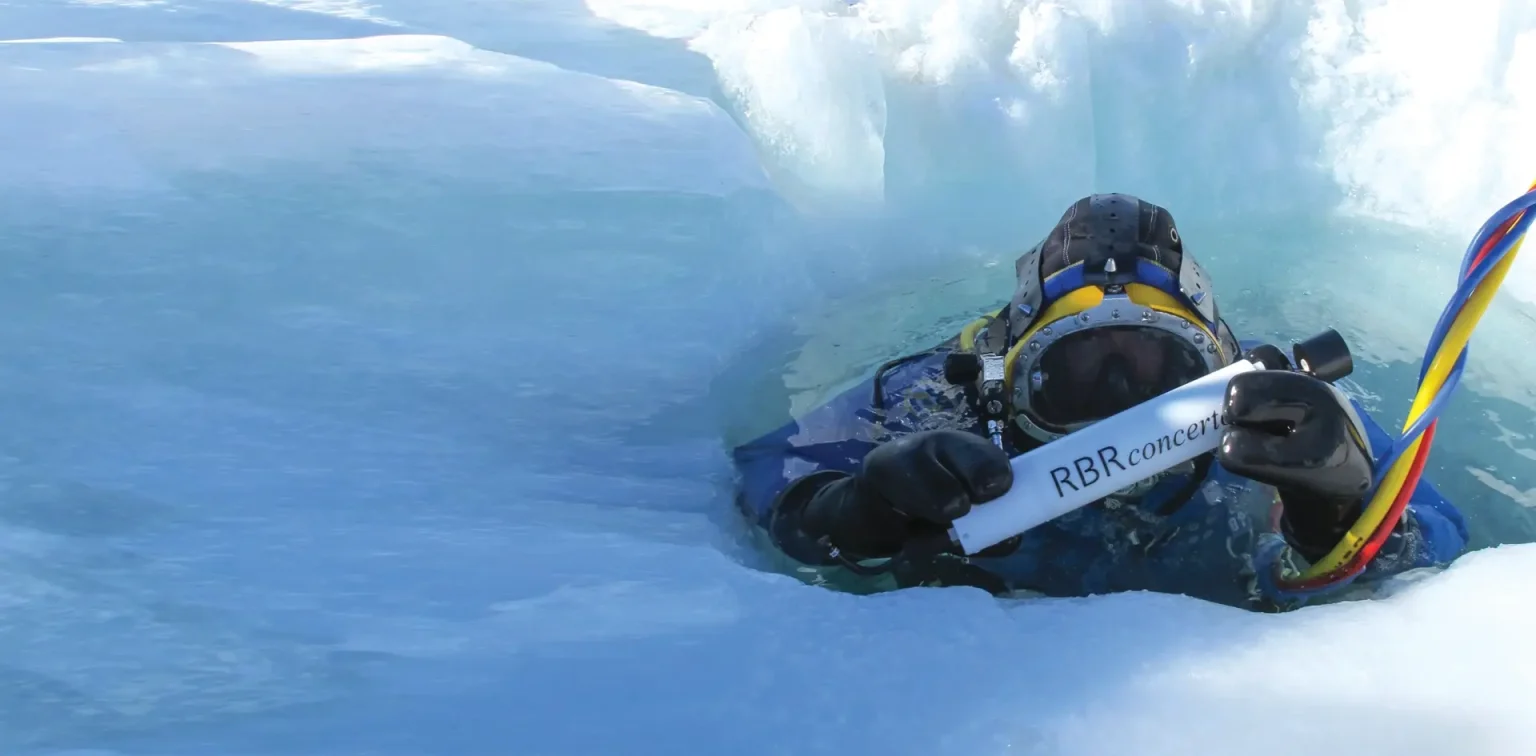